Mechanical Properties
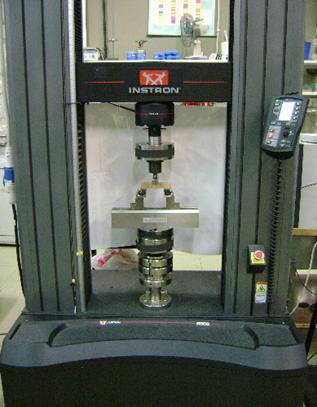
The laboratory is equipped with the Universal Mechanical Testing machine INSTRON 5982 (left) which offers the capability for loading all materials to 100kN (about 10 tons) under a range of different configurations to about 1300oC. We can test specimens of small to large size of various shape with simultaneous recording of their load-displacement electronically for further analysis. The loading rate varies from 1μm/min to 1000mm/min.
In particular, we can carry out the following measurements and tests:
1) Mechanical strength in compression, tension, bending (TRS/MOR) and shear.
2) Toughness and fracture toughness
3) Crack propagation development in real time
4) Crush resistance of brittle materials (rocks, ores etc)
5) Cyclic loading for determining fatigue resistance with a frequency up to 1Hz
6) Measurement of strain and of modulus of elasticity of various materials.
7) Special configurations for measurement of mechanical loading of e.g. pharmaceutical packages, electrical and electronic devices etc.
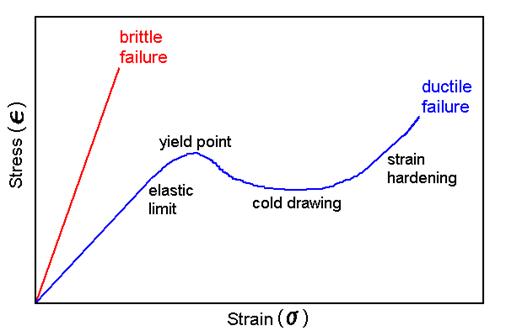
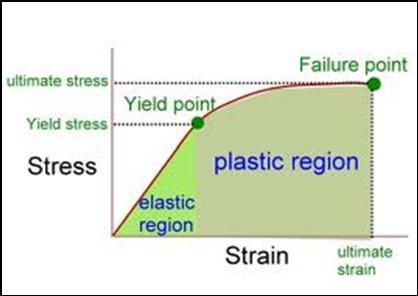
From the load-displacement curve obtained from the INSTRON and the geometric constants of the specimen, the stress-strain (σ-ε) characteristic can be calculated as shown schematically above for each material from which one can be calculate the strength (UTS etc), the yield point (metals) or crack initiation (brittle metals and ceramics) as well as other parameters, as indicated above.
The area under the σ-ε curve is a measure of the energy absorbed during fracture of a material and is thus a measure of the toughness, i.e. energy dissipation of a material.
In general, metals have a low yield point (load of first deformation) but high toughness and elongation to final fracture. This means that their plasticity gives them higher mechanical reliability compared to ceramics which fracture suddenly with relatively lower energy dissipation, albeit possibly at higher strength.
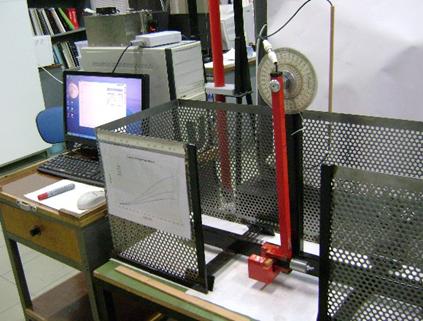
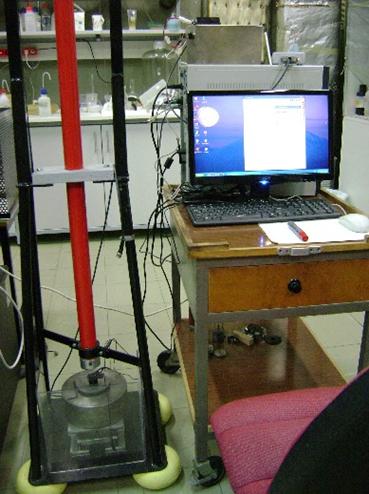
Impact strength of materials
From the load-displacement curve obtained from the INSTRON and the geometric constants of the specimen, the stress-strain (σ-ε) characteristic can be calculated as shown schematically above for each material from which one can be calculate the strength (UTS etc), the yield point (metals) or crack initiation (brittle metals and ceramics) as well as other parameters, as indicated above.
The area under the σ-ε curve is a measure of the energy absorbed during fracture of a material and is thus a measure of the toughness, i.e. energy dissipation of a material.
In general, metals have a low yield point (load of first deformation) but high toughness and elongation to final fracture. This means that their plasticity gives them higher mechanical reliability compared to ceramics which fracture suddenly with relatively lower energy dissipation, albeit possibly at higher strength.
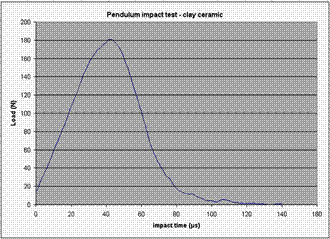
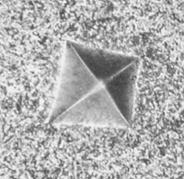
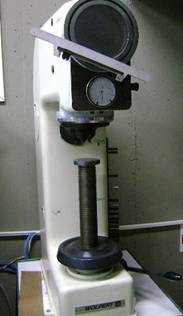
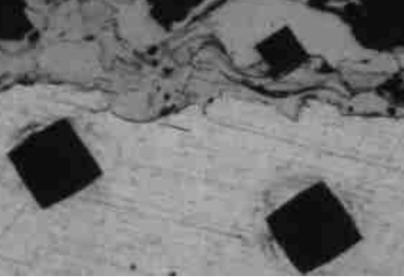
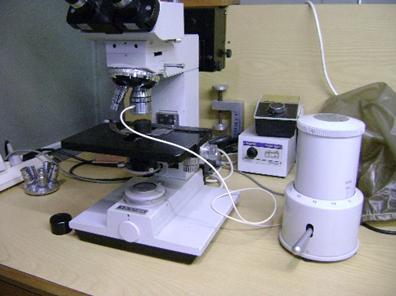
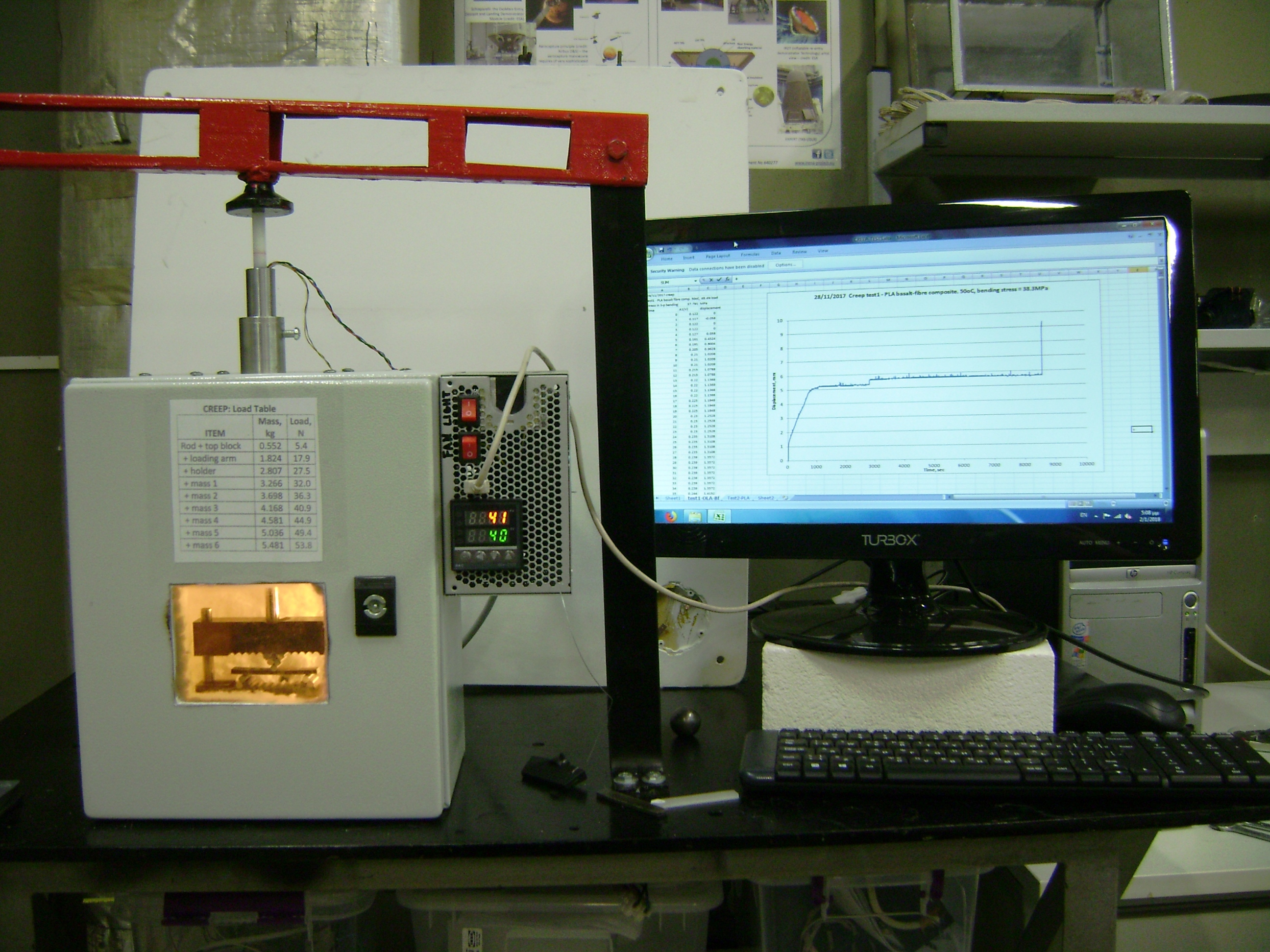
Creep is the slow deformation of materials under load at elevated temperatures and is used to characterise materials that are used under continuous loading. In our apparatus we can carry out creep testing under flexure of plastics and composites up to 200MPa and at temperatures up to 100oC, according to ASTM 2990. The deformation is recorded in real time for later analysis.
In the same apparatus, we are able to determine Heat Deflection Temperatures (HDT) of plastics and composites under flexure according to ISO 75.
Post-fatigue elastic modulus and remanent strength is an important industrial parameter for materials expected to be used under cyclical loading such as hinges, joints, inflatables. mobiles etc. In our low-cycle fatigue apparatus two specimens are subjected together to fatigue under flexure for thousands of cycles at a frequency up to about 1Hz and then tested to failure in the INSTRON to determine the effect of fatigue on their mechanical properties.
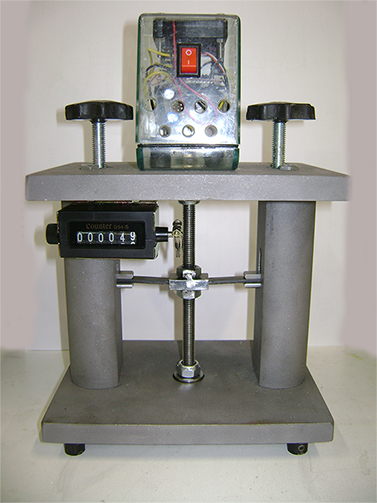